30 de noviembre de 2023 (Noticias de Nanowerk) Desde casas hasta audífonos, la impresión tridimensional (3D) está revolucionando la forma en que creamos estructuras complejas a escala. Acercándose a los niveles micro y nano, un proceso conocido como litografía de polimerización de dos fotones (TPL) permite a científicos e ingenieros construir objetos con precisión microscópica, lo que tiene implicaciones de amplio alcance para industrias que van desde la medicina hasta la manufactura. En informática y comunicaciones, por ejemplo, el TPL se puede utilizar para desarrollar nuevos materiales ópticos, como cristales fotónicos que pueden manipular la luz de nuevas formas. Sin embargo, a pesar de su promesa, todavía quedan algunos desafíos por delante para aprovechar plenamente su potencial. El principal de ellos es el desafío de lograr una contracción uniforme y tamaños de características por debajo de la longitud de onda de la luz visible, lo cual es esencial cuando se trata de manipulación avanzada de la luz. Para abordar este desafío, un equipo de investigadores dirigido por el profesor Joel Yang del pilar de Desarrollo de Productos de Ingeniería de la Universidad de Tecnología y Diseño de Singapur (SUTD), en colaboración con sus homólogos del Centro de Tecnología Industrial de la Prefectura de Wakayama en Japón, introdujo un nuevo método que Garantiza una contracción uniforme de las estructuras impresas en 3D cuando se tratan térmicamente. Esto refina aún más el uso de TPL en la producción de funciones a nanoescala de alta precisión. Su trabajo de investigación fue publicado en Nature Communications (“Proceso de selección y colocación para una contracción uniforme de materiales de micro y nano arquitectura impresos en 3D”).
La litografía de polimerización de dos fotones (TPL) está avanzando en la precisión en la creación de estructuras a micro y nanoescala, lo que afecta a múltiples industrias, desde la medicina hasta la fabricación.
Un equipo de la Universidad de Tecnología y Diseño de Singapur introdujo un método novedoso para la contracción uniforme de estructuras impresas en 3D, mejorando la precisión del TPL.
Esta técnica imita procesos naturales, similares a cómo se mueven las lombrices de tierra, para evitar la distorsión durante la contracción de los materiales impresos en 3D.
El nuevo proceso de reducción permite la creación de estructuras detalladas con características mejoradas y posibles nuevas funciones, como medidas contra la falsificación.
Las investigaciones futuras tienen como objetivo ampliar las aplicaciones de este método, mejorando potencialmente las tecnologías en campos como la electrónica, los sensores ópticos y los sistemas de imágenes.
Concepto y esquema del proceso de recogida y colocación para la contracción uniforme de micronanoestructuras impresas en 3D. (Imagen: SUTD)
Contracción uniforme del modelo 3D impreso con características (a, b) de microescala y (c) de nanoescala. Barra de escala: 20 µ 5 µm para las dos imágenes SEM inferiores derechas. (Imagen: SUTD) La tecnología desarrollada por el equipo de investigación es prometedora en industrias como la electrónica, donde se puede utilizar para fabricar intrincados disipadores de calor necesarios para enfriar dispositivos de alto rendimiento, como GPU y CPU de última generación. La contracción constante de los componentes impresos también abre aplicaciones en campos que requieren alta fidelidad en la estructuración de materiales, como piezas mecánicas con geometrías complejas, elementos ópticos con capacidades precisas de manipulación de la luz y dispositivos acústicos que pueden controlar el sonido con mayor precisión. De cara al futuro, los investigadores planean ampliar las aplicaciones de su técnica más allá del material de resina polimérica actual utilizado en su estudio. Al aplicar su método a materiales con índices de refracción más altos, su objetivo es crear cristales fotónicos más eficaces, lo que podría mejorar las tecnologías en láseres, sistemas de imágenes y sensores ópticos. Además, el equipo de investigación también está trabajando para perfeccionar el control del espaciado en estructuras impresas para producir modelos 3D a todo color que puedan controlar con precisión la forma en que se manipula la luz. Esto incluye esfuerzos para transferir y posicionar con precisión estas estructuras en áreas grandes o en cantidades significativas, manteniendo la alta precisión requerida para estas aplicaciones avanzadas.
Puntos clave
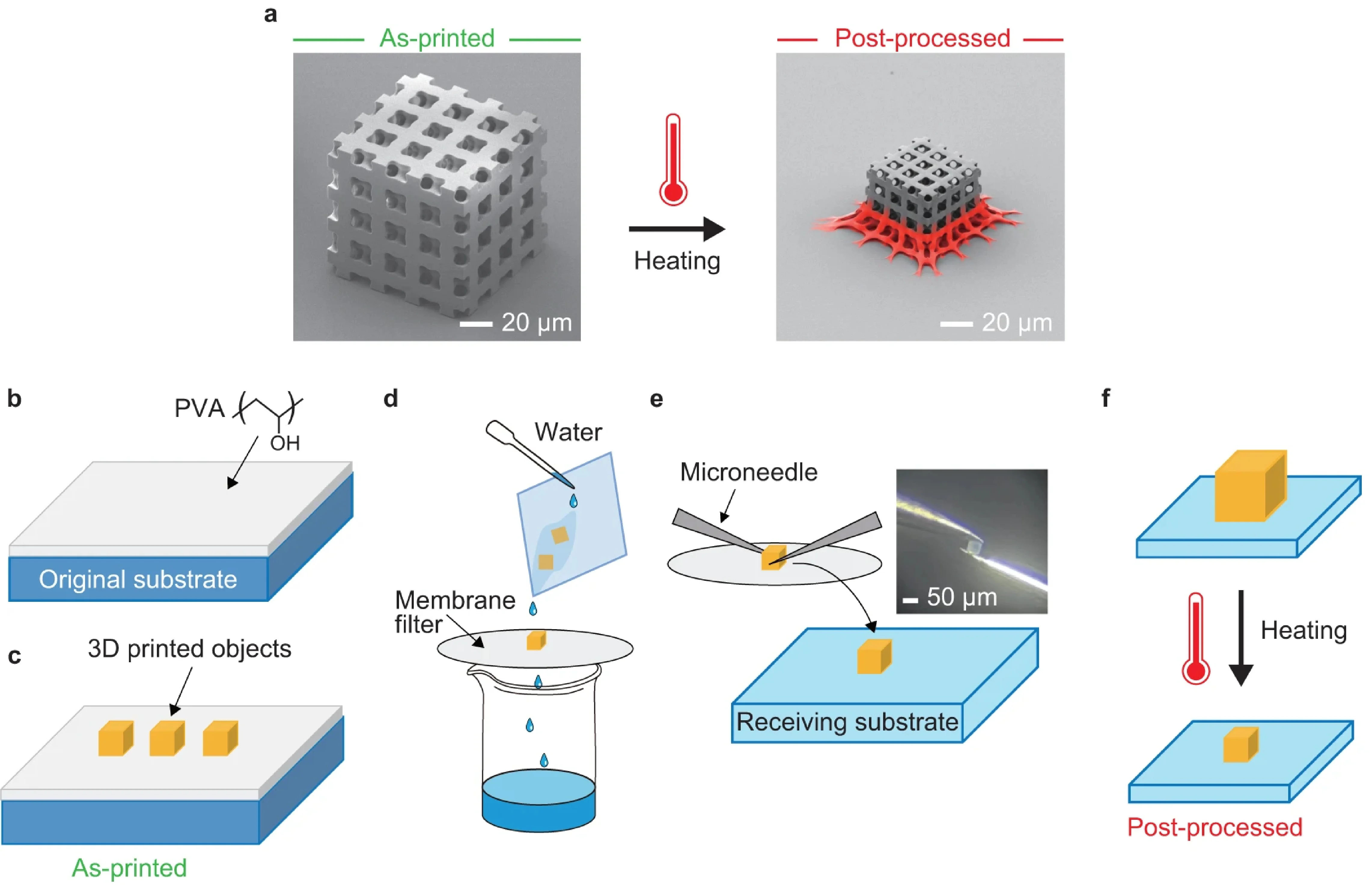
La investigación
En su estudio, los investigadores emplearon una capa de poli(alcohol vinílico), o PVA, sobre el sustrato de impresión para facilitar que las piezas impresas en 3D se laven y transfieran a un sustrato separado, permitiendo así una reducción controlada y uniforme de las piezas impresas en 3D. La unión suelta sobre el nuevo sustrato permitió que la base de las estructuras se deslizara mientras la impresión 3D general se contrae uniformemente durante el calentamiento. Este enfoque simple pero eficaz evita el problema de la contracción no uniforme causada por la unión de la estructura a la superficie sobre la que se imprimió. También abre posibilidades de transferir piezas microscópicas impresas en 3D para su integración con otros dispositivos o sobre sustratos que no son adecuados para TPL. El profesor Yang se inspiró en la naturaleza para esta técnica y afirmó: "Así como las lombrices de tierra se estiran y contraen para moverse a través de las superficies, creíamos que podríamos permitir que nuestras estructuras 3D se 'deslizaran' a un tamaño más pequeño sin distorsión". Según Tomohiro Mori, primer autor del artículo e investigador visitante del Centro de Tecnología Industrial de la prefectura de Wakayama, “la compleja geometría de la mascota de la prefectura de Wakayama, con sus diversas curvas, protuberancias y desniveles, la convirtió en un tema ideal para mostrar la efectividad de nuestra técnica. . La contracción uniforme exitosa de un modelo tan detallado sugiere que nuestro método podría adaptarse a cualquier forma, independientemente de su forma o de la solidez de la plataforma sobre la que se coloca". El enfoque del equipo permite la creación de estructuras finamente detalladas que superan lo que su equipo de impresión puede producir originalmente, rompiendo barreras previas de resolución y rigidez del material asociadas con los objetos impresos en 3D. Aprovechando este nuevo proceso de contracción, los investigadores también pueden refinar las características de las estructuras impresas en 3D hasta tal punto que puedan funcionar en nuevas funciones, como indicadores visuales debido a su capacidad para mostrar colores estructurales. Más importante aún, estos colores no se deben a tintes sino que surgen de la estructura interna del material que, cuando se reduce de tamaño, interactúa con la luz de una manera que altera su apariencia. Esto introduce nuevas funciones a los materiales. "Por ejemplo, incorporar en las estructuras ciertas moléculas llamadas cromóforos, que son sensibles a diferentes tipos de luz, podría permitirnos diseñar materiales que cambien de color en respuesta a condiciones de iluminación específicas", explicó el profesor Yang. "Esto tiene aplicaciones prácticas en la lucha contra la falsificación, donde se puede verificar la autenticidad de los artículos mediante distintos colores estructurales y las propiedades de emisión de estos materiales".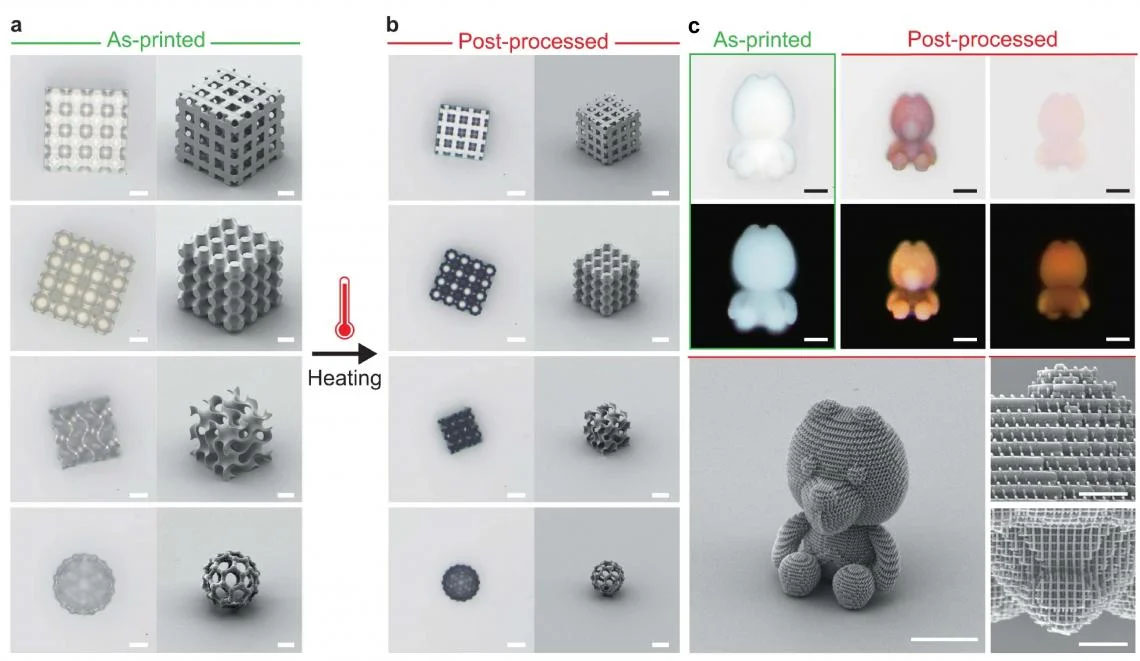
- Distribución de relaciones públicas y contenido potenciado por SEO. Consiga amplificado hoy.
- PlatoData.Network Vertical Generativo Ai. Empodérate. Accede Aquí.
- PlatoAiStream. Inteligencia Web3. Conocimiento amplificado. Accede Aquí.
- PlatoESG. Carbón, tecnología limpia, Energía, Ambiente, Solar, Gestión de residuos. Accede Aquí.
- PlatoSalud. Inteligencia en Biotecnología y Ensayos Clínicos. Accede Aquí.
- Fuente: https://www.nanowerk.com/news2/gadget/newsid=64150.php