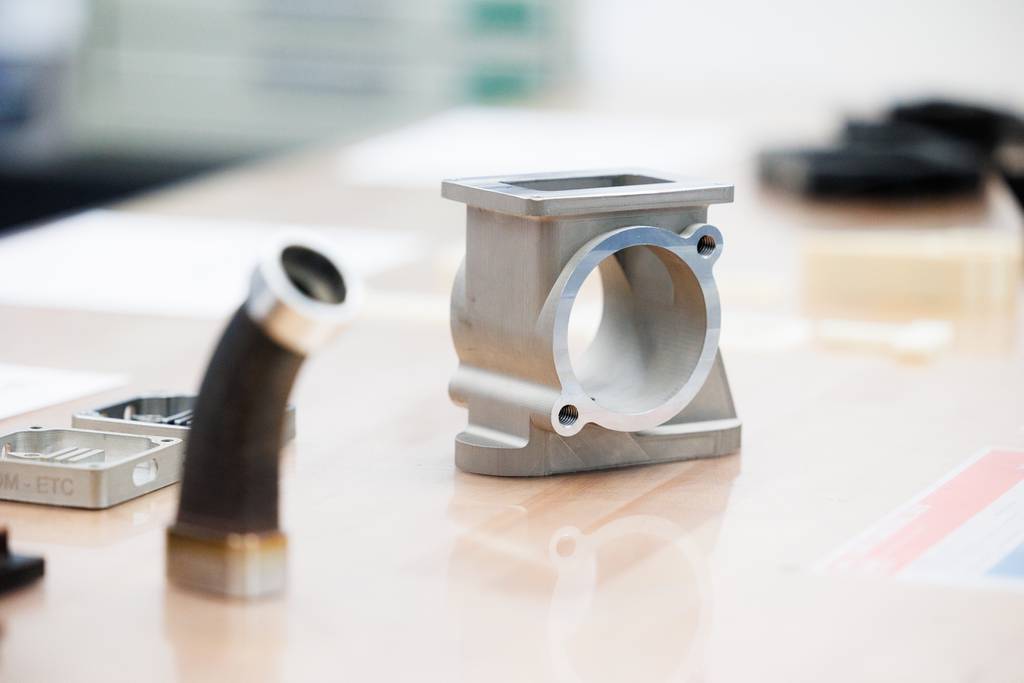
DANVILLE, Va. — Un nuevo edificio con fachada de vidrio se encuentra en un parque industrial prácticamente vacío aquí en la zona rural del sur de Virginia.
En el interior no hay vapor, humo ni hollín. No vuelan chispas. No se vierten metales calientes. No hay eco del golpe del martillo sobre el yunque.
Más bien, es todo blanco. Suelos blancos, paredes blancas, máquinas blancas que generan ruido blanco mientras imprimen y acaban pequeñas piezas metálicas. Está muy lejos de ser una fábrica tradicional que produce Componentes submarinos.
Pero los funcionarios de la Marina de los EE. UU. dicen que este edificio, el Centro de Excelencia de Fabricación Aditiva, representa el futuro de la industria submarina y quizás el único camino del servicio para construir a tiempo el submarino de misiles balísticos clase Columbia y el submarino de ataque clase Virginia.
La Armada ya ha utilizado la fabricación aditiva para imprimir pequeñas piezas de reparación en barcos en el mar, incluidas cubiertas de circuitos y botones de radio a los que sería difícil y costoso acceder para el servicio mientras están desplegados. Pero para el próximo año, a medida que la carga de trabajo para la base industrial de submarinos de EE. UU. alcance su nivel más alto en 40 años, la Armada imprimirá en 3D piezas metálicas como componentes estándar para su instalación en submarinos de nueva construcción.
Para cerrar la importante brecha entre el uso a pequeña escala de la fabricación aditiva hasta la fecha y la dependencia generalizada prevista en esta tecnología, la Marina ha encargado una serie de actividades para madurar la fabricación aditiva de metales, y Danville, Virginia, está en el centro de esa tarea. esfuerzo.
El Centro de Excelencia en Fabricación Aditiva busca ampliar la cadena de suministro de piezas submarinas ayudando a las empresas a adoptar la fabricación aditiva de metales.
Hay presión sobre la Marina para que esta tecnología funcione. ya el servicio gastó 2.3 millones de dólares para ampliar y fortalecer la base industrial submarina, y está dispuesto a gastar miles de millones más, siendo la fabricación aditiva una de las cinco áreas de enfoque de este gasto.
"Es una capacidad de fabricación imperativa" si la Marina y su base industrial tienen alguna posibilidad de aumentar la capacidad de construir un submarino clase Columbia y dos submarinos Virginia cada año durante la próxima década, dijo Matt Sermon, director ejecutivo de la Marina. Dirección Ejecutiva del Programa Submarinos Estratégicos.
El plan no está exento de riesgos, dicen los expertos.
"Se están logrando avances, pero todavía no es una tecnología de botón donde podamos decir: 'Haga esta pieza con este material y obtendrá lo que necesita'", dijo Kevin Jurrens, quien dirige el Instituto Nacional de Estándares. y el trabajo de la tecnología en la fabricación inteligente.
Las profundidades del desafío
La Armada está tratando de alcanzar un ritmo de construcción de submarinos no visto desde la década de 1980: está reemplazando simultáneamente su flota de submarinos con misiles balísticos y haciendo crecer una flota de submarinos de ataque que hoy tiene sólo el 75% del tamaño requerido por la Armada.
Sin embargo, la base industrial de las empresas que contribuyen a estos submarinos se ha reducido más del 70% desde la década de 1980, de unos 17,000 proveedores a 5,000. Y el aumento de la carga de trabajo se está produciendo relativamente rápido.
Tan recientemente como 2013, la Marina comenzaría a construir un submarino Virginia cada año. A partir del año fiscal 2026, la Marina planea realizar cinco veces ese trabajo (dos Virginia y el Columbia, mucho más grande, cada año), dada la complejidad de los submarinos.
Incluso el salto a dos submarinos Virginia al año hizo que la línea de construcción no cumpliera con los hitos, y hoy algunos barcos tienen un año o más de retraso debido a la pandemia de COVID-19. Los problemas relacionados con la logística y la fuerza laboral empeoraron los retrasos. La Marina ahora espera volver a realizar entregas a tiempo para el año fiscal 2028.
Pero el servicio dice que el submarino Columbia, de alta prioridad, no puede retrasarse.
El contralmirante Scott Pappano, director ejecutivo del programa de submarinos estratégicos que también supervisa el programa general de bases industriales de submarinos, dijo que la Armada enfrenta una batalla cuesta arriba. Aunque toda la carga de trabajo se quintuplicará, eso en realidad crea un aumento de diez veces para algunos sectores como el de fundición, que ya es un punto débil en la cadena de suministro.
Las piezas fundidas, o el vertido de metal caliente en moldes, se encuentran entre las áreas más desafiantes y pueden complementarse con la fabricación aditiva de metal.
"Sabemos dónde están nuestros sectores de mercado restringidos", dijo Pappano.
Whitney Jones, directora del programa de base industrial submarina de la Armada, dijo que los modelos internos muestran que ciertos componentes metálicos verán un aumento de hasta 6.4 veces en la demanda cuando la industria alcance su tasa máxima de construcción de submarinos.
La base industrial ya está detrás de la construcción de estas piezas metálicas: hoy en día, hay más de 100 piezas de los llamados materiales de secuencia crítica (lo que significa que retrasarán la construcción si no están disponibles) que se entregan con más de 300 días de retraso en promedio, pero son elegibles para ser impresos en 3D.
Imprimir estas piezas en lugar de fundirlas significaría que cada pieza tardaría menos en fabricarse y permitiría que más empresas las produjeran simultáneamente, reduciendo o eliminando retrasos tanto a nivel de proveedores como de astilleros.
Jones dijo que la fabricación aditiva de metal podría aumentar la capacidad de estas piezas metálicas entre un 15% y un 20% en dos o tres años, al tiempo que mejoraría la calidad y reduciría el tiempo de producción hasta en un 90%.
Al igual que con la impresión 3D de plástico, existen varios métodos para imprimir piezas metálicas. El más común y maduro utiliza un rayo láser para fundir polvo de metal que, capa por capa, crea la forma deseada basándose en un modelo digital.
Pappano dijo que la impresión 3D es el enfoque correcto.
“Tomo metal caliente y lo vierto en arena”, dijo sobre las piezas fundidas tradicionales. "Es muy medieval".
Pero con la fabricación aditiva, explicó, “puedo controlar las temperaturas del baño de soldadura y las tasas de deposición. … Puedo monitorear esa deposición, puedo buscar inconsistencias durante la construcción de la cosa y luego, en última instancia, puedo realizar pruebas no destructivas o pruebas destructivas para probar” su calidad.
Cómo imprimir piezas
En mayo, la Armada instaló un nuevo difusor de ventilación en el submarino de misiles balísticos Kentucky de clase Ohio. Esta pieza, que de otra manera no tendría nada de especial, una cubierta de ventilación metálica que dirige el flujo de aire, marcó la primera pieza metálica impresa que se instaló en un submarino.
Más recientemente, la Marina recurrió a la impresión 3D para una válvula del sistema sanitario en otro submarino de misiles balísticos en mantenimiento de depósito en Bangor, Washington. El fabricante original cerró y le habría llevado dos años conseguir una pieza similar a través del sistema de suministro tradicional.
En cambio, la Marina tomó una válvula existente, la escaneó con láser, realizó ingeniería inversa de la pieza en un sistema de diseño asistido por computadora, imprimió prototipos usando diferentes métodos, los probó y luego entregó la pieza final a Washington para su mecanizado e instalación finales.
En lugar de una fecha de entrega de marzo de 2025, la pieza estaba lista para una instalación en octubre de 2023.
Pero los funcionarios dicen que la Armada debe ir más allá de estos esfuerzos únicos y ampliar su trabajo para diseñar, calificar e instalar piezas impresas en submarinos.
Sermon dijo a Defense News que su oficina comenzó a examinar la fabricación aditiva después de ver que algunos proveedores usaban la tecnología. La oficina pasó el año pasado realizando experimentos a pequeña escala y “se convenció de que [la fabricación aditiva] no sólo podría, sino que debe representar, un aumento del 15[%] o del 20% en nuestra base industrial de fabricación de conformado de metales: piense en piezas fundidas, forjadas. , accesorios, sujetadores”.
La oficina se centra ahora en seis metales específicos que representan entre 15,000 y 20,000 componentes individuales necesarios para construir submarinos. Esa lista de piezas incluye el 75% de los componentes para nuevas construcciones y mantenimiento en servicio que son propensos a sufrir retrasos u otros desafíos. De hecho, tres de esos metales por sí solos representan el 50% de los retrasos en la fundición que afectan a la construcción de nuevos submarinos.
Aparte de los esfuerzos en Danville, Newport News Shipbuilding anunció recientemente su colaboración con el especialista en fabricación aditiva AMMCON Corp. para diseñar e imprimir un drenaje de cubierta de cobre y níquel para su instalación en el submarino de ataque clase Virginia Oklahoma y los barcos posteriores en la línea de producción, que representa el inicio de la inclusión de piezas impresas como un artículo estándar en la cadena de suministro. El cobre-níquel es una de las aleaciones clave con las que trabaja la Marina.
La Marina considera que estas piezas de bajo riesgo, como la válvula, el difusor de ventilación y la tapa del drenaje, son algo fácil de conseguir. Sermon señaló que alrededor del 20% de las piezas consideradas para la impresión 3D se consideran de bajo riesgo y podrían entrar en producción hoy.
Pero Pappano dijo que la Armada debe, en paralelo, madurar la tecnología para que pueda imprimir componentes relacionados con la integridad del casco, componentes relacionados con la energía nuclear y otras partes críticas.
Impresión bajo demanda
Para ampliar de manera tan significativa la producción de fabricación de metales, la Marina está trabajando con el estado de Virginia y socios de la industria en el Centro de Excelencia de Fabricación Aditiva para crear una red de socios de impresión y una cartera de pedidos digital para administrar la carga de trabajo.
Primero, el equipo crea los paquetes de datos técnicos, o “recetas”, para imprimir una pieza. Los miembros del equipo construyen, prueban y destruyen prototipos para perfeccionar la combinación de impresoras, procesos y aleaciones metálicas que crean las mejores piezas. Una vez que determinan el mejor proceso de impresión para ese tipo de pieza, finalizan el paquete de datos técnicos y buscan la certificación de la Marina.
Hasta la fecha, la Marina ha aprobado recetas para 28 piezas, incluida una variedad de válvulas, soportes, manijas, adaptadores y más.
Las instalaciones de Danville no producirán en masa esas piezas. En lugar de ello, serán transferidos a una creciente red de constructores.
Don Hairston, director general de Austal USA Advanced Technologies, que dirige el Centro de Excelencia de Fabricación Aditiva de la Marina, dijo que cuatro empresas han pasado por un extenso proceso para obtener la certificación de sus instalaciones, máquinas y empleados para formar parte de esta red. Cinco más serán “activados” (o certificados para unirse a la red) el próximo trimestre, y otros tres están en proceso.
En última instancia, dijo Hairston a Defense News, la Marina prevé una red de 50 o más sitios en los Estados Unidos que impriman piezas metálicas para la construcción de nuevos submarinos. También podría haber más en el Reino Unido y Australia para contribuir a la acuerdo trilateral AUKUS, agregó.
Hairston dijo que lo que el centro llama un libro de pedidos digital automatizará el proceso de pedido de piezas. Por ejemplo, cuando la Marina realiza un pedido de 200 válvulas de bola de 3/8 de pulgada, el equipo de Hairston en el centro de excelencia podrá ver qué proveedores de la red tienen el proceso de impresión y el metal adecuados para la receta de esa válvula. Entre los proveedores calificados, el equipo también podrá ver quién tiene la capacidad para el trabajo.
El libro de pedidos digital es un trabajo en proceso, dijo Hairston, pero está en camino de entrar en funcionamiento a fines de 2024. Para entonces, la Marina debería tener 15 socios de impresión en la red y al menos entre 150 y 200 piezas con características técnicas aprobadas. paquetes de datos, señaló.
Una carrera contra el tiempo
La Armada necesita comenzar a imprimir en masa estas piezas lo antes posible, según Jones, director del programa de base industrial submarina de la Armada.
“Estamos a dos años de tener que estar en un Columbia y dos Virginia al año, y si no tomamos medidas audaces que asuman algún nivel de riesgo compartido, no llegaremos allí cuando necesitemos estar allí. , y eso conlleva un tipo de riesgo completamente diferente”, dijo.
Pero los expertos técnicos argumentan que la tecnología no está del todo disponible, particularmente teniendo en cuenta los altos estándares involucrados en el trabajo submarino. Jurrens, cuya oficina del NIST está desarrollando estándares para guiar los esfuerzos de garantía de calidad para técnicas de fabricación avanzadas, dijo que la calificación y certificación para la fabricación aditiva siguen siendo barreras importantes.
Hoy, explicó, una empresa de fabricación aditiva tendría que calificar el material, el proceso, la máquina y el operador, para luego certificar la pieza final. Cualquier cambio, como que un nuevo empleado use la impresora, reiniciaría el proceso de calificación.
“Llegar a ese paso calificado requiere mucho tiempo y mucho trabajo”, dijo Jurrens. "Para realizar calificaciones aceleradas a través de cosas como la simulación y otras técnicas, esas capacidades están mejorando, pero no han llegado al punto en que los usuarios finales y las partes interesadas quieran confiar en ellas".
También hay dudas sobre cómo garantizar la calidad de la parte final.
Ron Aman, líder senior de tecnología de fabricación aditiva en la organización sin fines de lucro de investigación y desarrollo EWI, dijo que existen procesos aprobados para encontrar y reparar defectos en una pieza de metal fundido, pero todavía existe preocupación y confusión sobre cómo hacerlo en una pieza impresa.
Una tendencia creciente, y que la Marina está utilizando en su centro de excelencia, es instalar cámaras, sensores y micrófonos para monitorear el proceso de impresión e identificar defectos en tiempo real.
“No queremos hacer dos partes y luego romper una [en pruebas destructivas] y luego decir: 'Ah, creemos que la otra es buena'. Lo que queremos hacer es formar parte, queremos observar muy de cerca lo que estamos haciendo y obtener esa confianza, y luego usar lo que aprendimos de las señales del proceso para informar nuestros criterios de inspección”, dijo Aman.
Eso es algo en lo que está trabajando Sandra DeVincent Wolf, directora ejecutiva del Manufacturing Futures Institute de la Universidad Carnegie Mellon. Las máquinas de sus laboratorios están equipadas con sensores: cámaras de alta y baja velocidad, imágenes térmicas, imágenes del charco de fusión, imágenes de las salpicaduras de metal, monitoreo acústico y más.
En todos estos se encuentran signos de defectos y, dependiendo de la situación, la impresión podría detenerse y el operador comenzar de nuevo, o se podría anotar el defecto para su posterior inspección y reparación.
Dijo que el objetivo es llegar al punto en el que no todos los elementos requieran pruebas al final. Debido a la mayor confianza en los sistemas de seguimiento, tal vez sólo uno de cada 10 podría someterse a pruebas de calidad al final, añadió Wolf, y eventualmente uno de cada 100.
Otro obstáculo técnico clave se relaciona con los tipos de impresoras que utilizará la Marina. John Harrison, vicepresidente senior de trabajo global de aditivos en Phillips Corp., uno de los principales socios del centro de excelencia, dijo que uno de los procesos de impresión más maduros y confiables, la fusión de lecho de polvo, sólo puede fabricar piezas más pequeñas.
Otras técnicas, como la deposición de energía dirigida por arco de alambre, la deposición de energía dirigida por láser y la fabricación aditiva por fricción y agitación, pueden fabricar piezas más grandes, pero estas tecnologías son más nuevas, lo que significa que hay menos datos sobre la calidad de sus productos finales, dijo.
Sermon de PEO Strategic Submarines dijo que su oficina está trabajando en un esfuerzo "improvisado" para imprimir piezas muy grandes (piezas críticas relacionadas con la integridad del casco) que incluso hace un año se consideraban imposibles de imprimir. Con base en los resultados de las pruebas de esas grandes piezas impresas, la Marina determinará si puede utilizar métodos más nuevos para imprimir componentes grandes.
Incorporar a la industria
Ninguno de los planes de la Armada para ampliar su capacidad de fabricación de metales mediante la fabricación aditiva funcionará si la industria no comienza a imprimir para la base industrial submarina.
Josh Cramer, director de educación y desarrollo laboral de La asociación público-privada America Makes, afiliada al Departamento de Defensa, dijo que hay una escasez de 50,000 personas en la fuerza laboral de fabricación aditiva y que la demanda de estos trabajadores aumentará en los próximos años.
"Tenemos que incorporar más personas a la industria en general porque no tenemos suficientes humanos para siquiera capacitarlos para desempeñar esos roles", dijo.
America Makes está trabajando en una campaña de divulgación para concienciar a los trabajadores potenciales no solo de los empleos disponibles dentro del sector de fabricación aditiva, sino también de la capacitación y educación necesarias para cada trabajo y dónde conseguirlas.
Algunos de los constructores navales más conocidos ya están incursionando en la fabricación aditiva.
El portavoz de General Dynamics Electric Boat, Daniel McFadden, dijo que el astillero está trabajando para reclutar "nuevos proveedores expertos en fabricación de aditivos que ingresen a la base industrial submarina y desarrollen capacidad [aditiva] con los proveedores existentes cuando tenga sentido para la línea de productos".
La empresa quiere contribuir al esfuerzo continuo para definir procedimientos y pruebas aprobados para la impresión 3D para poder recurrir a piezas impresas en su cadena de suministro, "particularmente para piezas de mayores consecuencias donde la escasez y los largos plazos de entrega son un factor limitante para la producción". .”
John Wilczynski, director ejecutivo de America Makes, dijo que la organización también está intentando expandir el ecosistema de impresión 3D. Si bien invertir en impresoras y en capacitación del personal o nuevos empleados tiene un costo inicial, dijo Wilczynski, la magnitud de la carga de trabajo de construcción de submarinos en los próximos años crea una clara señal de demanda para las empresas que se preguntan si verán un retorno de su inversión. .
"No se puede evitar la narrativa de dos más uno en este momento", dijo, refiriéndose a las tasas de producción de los submarinos de las clases Virginia y Columbia. “Es muy evidente para todos que se trata de un riesgo importante para la defensa nacional. Hay poder en eso porque se está volviendo más visible para las personas que pueden estar tratando de decidir hacia dónde llevarán su negocio a continuación”.
Megan Eckstein es la reportera de guerra naval en Defense News. Ha cubierto noticias militares desde 2009, con un enfoque en las operaciones, los programas de adquisición y los presupuestos de la Armada y el Cuerpo de Marines de EE. UU. Ha informado desde cuatro flotas geográficas y es más feliz cuando presenta historias desde un barco. Megan es alumna de la Universidad de Maryland.
- Distribución de relaciones públicas y contenido potenciado por SEO. Consiga amplificado hoy.
- PlatoData.Network Vertical Generativo Ai. Empodérate. Accede Aquí.
- PlatoAiStream. Inteligencia Web3. Conocimiento amplificado. Accede Aquí.
- PlatoESG. Carbón, tecnología limpia, Energía, Ambiente, Solar, Gestión de residuos. Accede Aquí.
- PlatoSalud. Inteligencia en Biotecnología y Ensayos Clínicos. Accede Aquí.
- Fuente: https://www.defensenews.com/industry/techwatch/2023/11/06/manufacturing-woes-could-sink-us-sub-fleet-can-3d-printing-save-it/