28 de octubre de 2023 (Proyector Nanowerk) Desde los vívidos azules y verdes de las plumas de pavo real hasta los brillantes rojos de los cristales de rubí, el color estructural en la naturaleza proporciona algunas de las exhibiciones más deslumbrantes que deleitan nuestros ojos. A diferencia de los pigmentos que absorben ciertas longitudes de onda para producir color, el color estructural surge de la interacción física de la luz con características a nanoescala de un material. Esto hace que estos materiales "fotónicos" sean más sostenibles, resistentes al blanqueamiento y permiten una sintonización dinámica. Sin embargo, darles forma de complejas geometrías 3D sigue siendo un desafío duradero. Se ha demostrado que la impresión 3D es un método eficaz para fabricar cristales fotónicos: materiales con nanoestructuras periódicas que controlan la propagación de la luz mediante la creación de bandas prohibidas fotónicas. Pero los cristales fotónicos dependen de un orden de largo alcance y se han limitado a formas más simples mediante la impresión. Ahora, investigadores de ETH Zurich han aprovechado la técnica de impresión 3D con procesamiento digital de luz (DLP) para crear vidrios coloidales fotónicos estructuralmente coloreados con geometrías complejas y propiedades de color personalizadas.
Esquemas del flujo de trabajo utilizado para la fabricación de vidrios coloidales fotónicos de formas complejas mediante impresión 3D DLP. a – d) Formulación de resina típica que comprende partículas coloidales de sílice suspendidas en una mezcla de monómeros fotorreactivos. e,f) Caricaturas del principio de funcionamiento del proceso de impresión DLP destacando las microestructuras de objetos 3D de formas complejas después de la impresión de la resina y la calcinación de las piezas impresas. (Reimpreso con autorización de Wiley-VCH Verlag) Su trabajo, publicado en Materiales avanzados (“Impresión 3D basada en luz de gafas coloidales fotónicas de formas complejas”), demuestra cómo la combinación de materiales diseñados racionalmente y la fabricación aditiva puede ampliar el espacio de diseño para dispositivos fotónicos. Los investigadores se centraron en los vidrios fotónicos, una clase de materiales fotónicos desordenados que contienen nanopartículas de tamaño controlado que interactúan con la luz para producir un color estructural sostenible y no iridiscente que se puede ajustar en todo el espectro visible. La combinación de orden de corto alcance y desorden de largo alcance conduce a un color estructural vívido y no iridiscente. Para crear dichos materiales, el equipo comenzó con una resina personalizada que contenía monómeros reticulables, fotoiniciadores y nanopartículas de sílice. Utilizando una impresora 3D DLP comercial, solidificaron esta resina líquida en objetos 3D curándola capa por capa mediante proyección de luz. El paso clave vino a continuación: el calentamiento a alta temperatura de 400 C transformó la matriz polimérica impresa en un material vítreo con el orden estructural deseado. El equipo demostró que podían controlar el color del material final ajustando el tamaño de las nanopartículas de sílice a 200, 350 y 300 nm para obtener tonos azules, verdes o rojos respectivamente. Los análisis detallados de espectroscopía y microscopía electrónica revelaron que el color observado se debía a la dispersión selectiva de la luz por parte de las nanopartículas ordenadas localmente pero desordenadas globalmente. La comparación de las longitudes de onda máximas reflejadas con las predicciones teóricas confirmó este mecanismo. Un problema que el equipo tuvo que controlar cuidadosamente fue evitar la dispersión múltiple que destruiría la pureza del color. Lo lograron mediante protocolos de calcinación que dejaron una cantidad ideal de residuo de carbono: suficiente para limitar la profundidad de penetración pero no demasiado para permitir la reflexión en la superficie. Armados con la capacidad de prescribir colores y formas, los investigadores imprimieron complejas arquitecturas 3D a escala de centímetros. Se demostraron redes multimateriales con regiones definidas con precisión de rojo, verde y azul. Al modular espacialmente las geometrías del andamio, se codificaron variaciones de color graduadas en armazones de octetos 3D durante el mismo paso de pirólisis. Para resaltar la libertad de configuración de la impresión 3D, el equipo también fabricó réplicas fotónicas de artefactos culturales.
Vidrios coloidales fotónicos de formas complejas fabricados mediante impresión DLP. a, b) Ejemplos de celosías de panal y octeto-truss que presentan distintos colores estructurales dependiendo del tamaño de partícula utilizado en la resina inicial. Las imágenes muestran fotografías de las redes 3D antes (izquierda) y después (derecha) de la calcinación de resinas con partículas de sílice monodispersas con tamaños promedio de 300, 250 y 200 nm (de izquierda a derecha). c) Red multimaterial estructuralmente coloreada con arquitectura de panal obtenida mediante impresión DLP y calcinación de resinas que contienen partículas de sílice de 200, 250 y 300 nm. d) Redes de octeto-truss diseñadas para mostrar un gradiente de color en direcciones específicas ajustando los tamaños de las celdas y, por lo tanto, la permeabilidad local de la estructura al oxígeno durante la calcinación. Barras de escala: 5 mm. (Reimpreso con autorización de Wiley-VCH Verlag) Los resultados establecen que la fabricación aditiva basada en DLP es una ruta prometedora para diseñar componentes fotónicos de formas complejas. El acceso a colores estructurales complejos no iridiscentes puede beneficiar las aplicaciones de detección colorimétrica, lucha contra la falsificación, visualizaciones y camuflaje. Desde la perspectiva de los materiales, la técnica basada en la calcinación ofrece una formación de color sostenible simplemente utilizando sílice y carbono. Ampliar el rango visible actual a UV o infrarrojo podría permitir aplicaciones adicionales en espectroscopia, imágenes e interacciones hombre-máquina. Al combinar el diseño racional y la fabricación avanzada, este estudio destaca el potencial futuro de la producción aditiva para dispositivos fotónicos estructuralmente complejos.
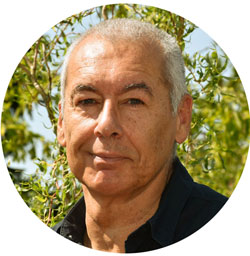
By
Michael
Berger
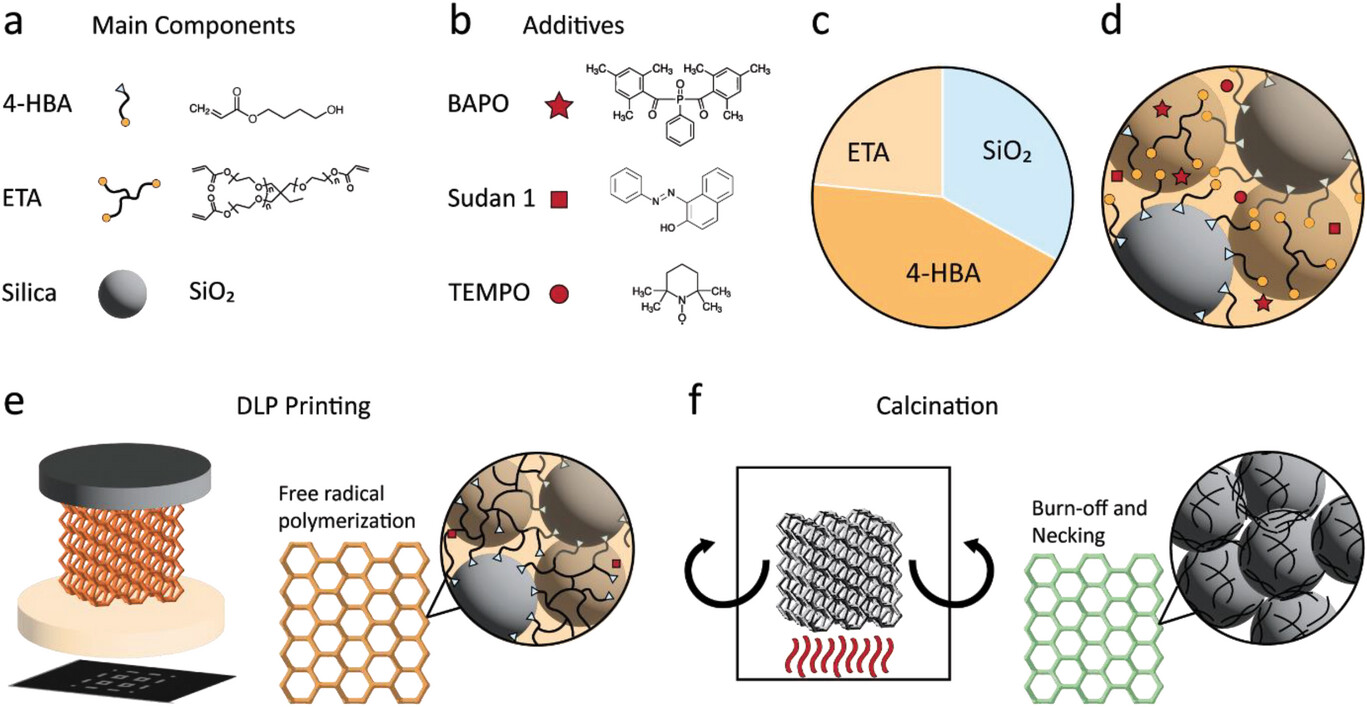
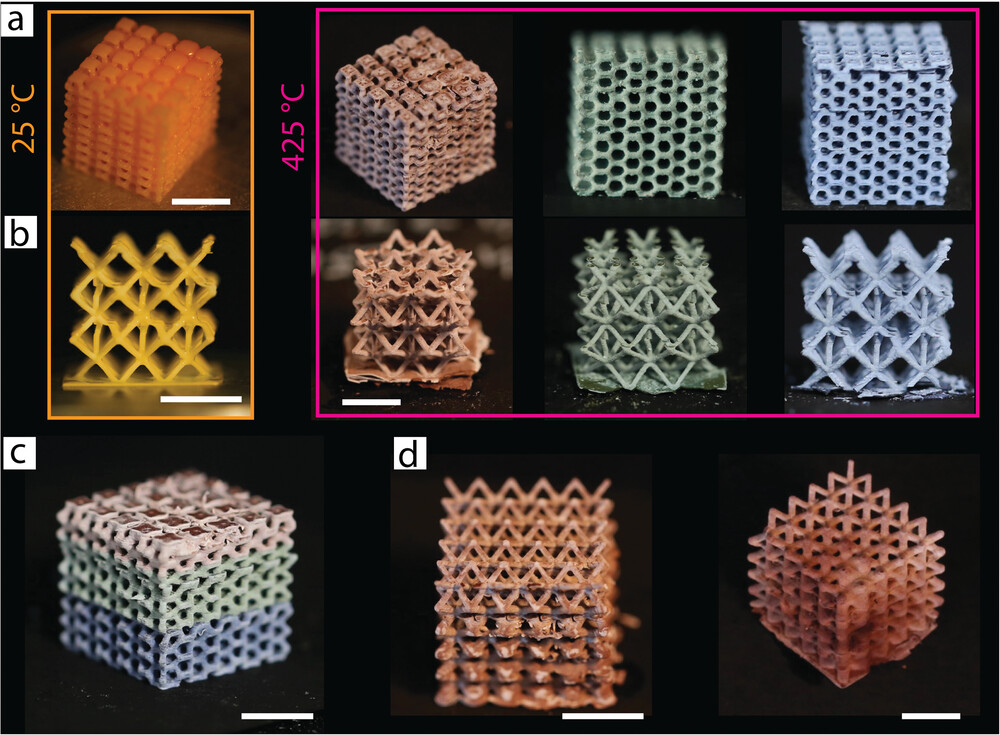
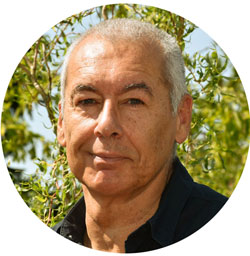
By
Michael
Berger
– Michael es autor de tres libros de la Royal Society of Chemistry:
Nano-sociedad: empujando los límites de la tecnología,
Nanotecnología: el futuro es pequeñoy
Nanoingeniería: las habilidades y herramientas que hacen que la tecnología sea invisible
Copyright ©
Nanowerk LLC
¡Conviértete en autor invitado de Spotlight! Únase a nuestro gran y creciente grupo de contribuyentes invitados. ¿Acaba de publicar un artículo científico o tiene otros desarrollos interesantes para compartir con la comunidad de nanotecnología? Aquí se explica cómo publicar en nanowerk.com.
- Distribución de relaciones públicas y contenido potenciado por SEO. Consiga amplificado hoy.
- PlatoData.Network Vertical Generativo Ai. Empodérate. Accede Aquí.
- PlatoAiStream. Inteligencia Web3. Conocimiento amplificado. Accede Aquí.
- PlatoESG. Carbón, tecnología limpia, Energía, Ambiente, Solar, Gestión de residuos. Accede Aquí.
- PlatoSalud. Inteligencia en Biotecnología y Ensayos Clínicos. Accede Aquí.
- Fuente: https://www.nanowerk.com/spotlight/spotid=63956.php