Diferentes requisitos
En las empresas manufactureras, las tiradas de producción se han acortado, debido en parte a la necesidad real o imaginaria de extensiones de productos que aborden las necesidades específicas de los clientes y consumidores. Hay menos fabricación contra stock (MTS) de alto volumen y más mezcla alta, volumen bajo (HMLV) en los descriptores de fabricación bajo pedido (MTO) y ensamblaje bajo pedido (ATO). Esto puede influir en la planificación de los fabricantes contratados, la producción subcontratada, los proveedores y los 3PL.
En cualquier situación en la que una empresa ofrezca más artículos o unidades de mantenimiento de existencias (SKU) para un producto determinado, habrá más competencia por los recursos operativos y, por lo tanto, variabilidad en la utilización de los recursos. Para lograr operaciones más efectivas es necesario centrarse en la capacidad: de instalaciones, máquinas, personas y suministros de insumos.
La necesidad es diferenciar la Planificación y Programación entre el horizonte de decisiones, la disponibilidad de tiempo de la gestión y el volumen de datos e información a analizar y considerar. La planificación es táctica y se ocupa principalmente de las personas y su voluntad de colaborar. Esto es para permitir un entendimiento común sobre el futuro e identificar y acordar resultados. Sin embargo, la programación es operativa y se ocupa de cualquier recurso que pueda afectar la producción productiva (es decir, máquinas y sus accesorios, personas y suministros) y, por lo tanto, debe tener un cronograma de uso detallado.
Un plan
Aunque tenga diferentes necesidades de tiempo y datos, el proceso de planificación y programación debe estar contenido dentro del enfoque de 'Plan único', que se muestra en el diagrama.
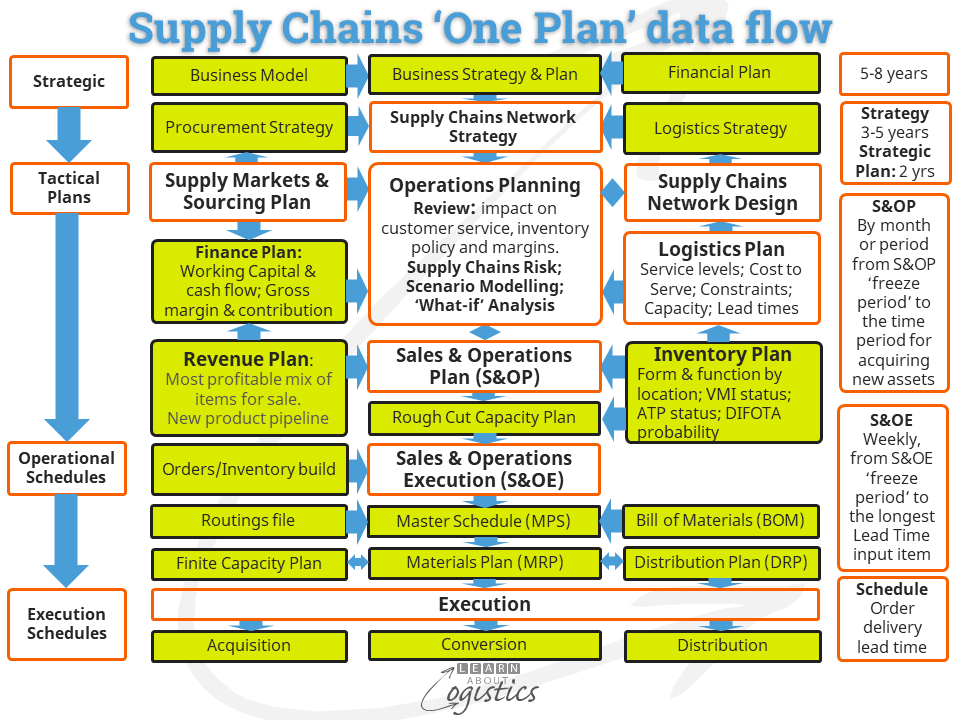
Aunque los datos base siguen siendo los mismos, el nivel de granularidad cambia en cada etapa del flujo del proceso:
- El horizonte del proceso de Planificación de Operaciones y Ventas (S&OP) comienza en el tercer mes (o período tres, cada uno de 4 semanas). El mes/período uno y dos (el período de 'congelación') ya se han programado dentro del proceso de Ejecución de Ventas y Operaciones (S&OE). Por lo tanto, S&OP se lleva a cabo a un nivel consolidado de detalle como se analiza en el blog anterior. En este caso, la medida de capacidad utilizada es la 'demostrado' capacidad; es decir, el rendimiento actual de una máquina o línea de producción, teniendo en cuenta eventos no planificados, como averías e interrupciones. Además, incluya el tiempo de cambio entre corridas de producción. Por ejemplo, en una línea de producción de plásticos, el tiempo de cambio de negro a blanco es mucho más largo (debido a un lavado) que de blanco a negro. En la alimentación, el paso del chocolate con leche al negro es más corto que del chocolate negro al con leche.
- Dentro de Ejecución de Ventas y Operaciones (S&OE), el horizonte para los cronogramas operativos es desde el período de "congelación" de programación actual (que podría ser las próximas dos semanas) hasta el tiempo de entrega más largo de los materiales comprados y artículos intermedios. Los cronogramas de operaciones requieren información detallada para ser efectivos: la tarea, los recursos (máquinas y personas) necesarios y el tiempo para completar las tareas. Además, en este nivel se encuentra el potencial de conexión de equipos para la recolección de datos en línea vía sistemas SCADA (supervisión, control y adquisición de datos), a través del Internet Industrial de las Cosas (IIoT). El rendimiento del equipo se puede perfilar y analizar para que el mantenimiento programado se incorpore al cronograma operativo; también como entrada para la simulación de operaciones de 'gemelo digital'.
- Para los cronogramas de ejecución, el horizonte es el tiempo de entrega de los pedidos de los clientes actuales. Para tener en cuenta las interrupciones y retrasos en la producción y aun así cumplir con el cronograma de Operaciones, el cronograma de Ejecución puede tener algunos pedidos comenzando temprano y otros comenzando tarde, para alinearse con la disponibilidad de recursos.
- Los cronogramas operativos y de ejecución deben estar vinculados al sistema Disponible para prometer (ATP), por lo que existe "una fuente de verdad" con respecto a la disponibilidad actual de los SKU para su uso en pedidos en línea y por parte del personal de servicio al cliente.
Vínculo entre planificación y programación
El vínculo entre la planificación y los cronogramas es la lista de materiales. Esto se construye para cada producto o unidad de mantenimiento de existencias (SKU) y define (en una cantidad por base) los materiales y bienes intermedios utilizados. La ruta más los tiempos de configuración y operación se definen en función de los datos del archivo de rutas. Los campos de la lista de materiales identifican la 'familia' de SKU (o cadena de suministro) que se utilizará en el proceso S&OP. Además, la capacidad de convertir la medida del SKU (peso, volumen, embalaje, etc.) a la unidad de medida estándar utilizada para S&OP (toneladas, litros, envío estándar, etc.).
Esta capacidad permite que el Plan de S&OP (puede ser el Plan de capacidad preliminar (RCCP) dentro del sistema ERP) se ingrese en el Programa maestro de S&OE como un pronóstico para los períodos futuros aplicables. Para hacer esto, el S&OP durante el horizonte de planificación se desagrega en SKU individuales, según porcentajes de ventas históricos.
Como la BoM requiere la 'cantidad por' para cada material suministrado y bienes intermedios, el S&OP puede planificar los requisitos de materiales para ingresar al proceso de Gestión de categorías de adquisiciones. En el proceso S&OE, el Plan de Requerimientos de Materiales proporciona un cronograma para la adquisición de insumos contratados.
Capacidad de programación
El desafío ocurre a la hora de programar la capacidad. El enfoque tradicional (y la construcción del software) se basa en el concepto de capacidad infinita utilizado para el RCCP. Al programar operaciones, el software asume que hay capacidad infinita y solo indica cuando se excede la capacidad, confiando en que las personas hagan los ajustes necesarios. Esto permite una implementación y un uso relativamente fáciles, lo cual es aceptable para RCCP debido al largo horizonte utilizado en S&OP.
Sin embargo, la programación de operaciones requiere una programación finita que conozca las limitaciones de capacidad. Para hacer esto se requiere (al menos) la actualización y el ingreso de: reglas de secuencia operativa (por ejemplo, la secuencia de colores a utilizar o transferir el tamaño del lote a la siguiente operación); ruta alternativa; rendimiento de la máquina; tiempos de preparación de la máquina; reglas de prioridad del cliente.
El resultado de una rutina de programación de capacidad finita será una secuencia de actividades y tareas en cada centro de trabajo de la instalación. El Cronograma de Operaciones para el actual período se mantiene firme; sin embargo, el Cronograma de Ejecución (que comienza como una copia del Cronograma de Operaciones) se puede ajustar para cumplir con las condiciones actuales, con algunos trabajos comenzando temprano y otros tarde, pero el resultado del Cronograma es el objetivo.
Un modelo de operaciones de fabricación o ensamblaje bajo pedido requiere la capacidad de programar con precisión una variedad de productos en cantidades de pedido relativamente pequeñas. Pero la variedad adicional de productos requerida con tiempos de respuesta más rápidos puede aumentar los costos. Por lo tanto, no es aconsejable utilizar la rutina de programación infinita que puede incorporarse en un sistema ERP. En cambio, el requisito es una aplicación de programación finita que pueda interactuar con el sistema ERP actual.
- Distribución de relaciones públicas y contenido potenciado por SEO. Consiga amplificado hoy.
- PlatoData.Network Vertical Generativo Ai. Empodérate. Accede Aquí.
- PlatoAiStream. Inteligencia Web3. Conocimiento amplificado. Accede Aquí.
- PlatoESG. Carbón, tecnología limpia, Energía, Ambiente, Solar, Gestión de residuos. Accede Aquí.
- PlatoSalud. Inteligencia en Biotecnología y Ensayos Clínicos. Accede Aquí.
- Fuente: https://www.learnaboutlogistics.com/the-scheduling-part-of-operations-planning-and-scheduling/#utm_source=rss&utm_medium=rss&utm_campaign=the-scheduling-part-of-operations-planning-and-scheduling